Service Propulsion System: Difference between revisions
imported>Tschachim |
imported>Tschachim (Removed Standard mode) |
||
(27 intermediate revisions by 3 users not shown) | |||
Line 1: | Line 1: | ||
[[Image:SPS diagram.jpg|thumb|right|250px|The Service Propulsion System<cite>CSMNEWSREF</cite>]] | [[Image:SPS diagram.jpg|thumb|right|250px|The Service Propulsion System<cite>CSMNEWSREF</cite>]] | ||
The '''Service Propulsion System (SPS)''' is the [[Command/Service Module]] main engine and provides the impulse for all velocity changes (ΔVs) throughout a mission and the SPS abort capability after the launch escape tower is jettisoned. The engine uses [[w:Aerozine 50|Aerozine 50]] ([[w:hydrazine|hydrazine]]/[[w:UDMH|UDMH]]) fuel and [[w:nitrogen tetroxide|nitrogen tetroxide]] [[w:oxidizer|oxidizer]] and has a | The '''Service Propulsion System (SPS)''' is the [[Command/Service Module]] main engine and provides the impulse for all velocity changes (ΔVs) throughout a mission and the SPS abort capability after the launch escape tower is jettisoned. The engine uses [[w:Aerozine 50|Aerozine 50]] ([[w:hydrazine|hydrazine]]/[[w:UDMH|UDMH]]) fuel and [[w:nitrogen tetroxide|nitrogen tetroxide]] [[w:oxidizer|oxidizer]] and has a nominal thrust of 20,500 lbf (91.2 kN)<cite>I</cite>. This [[w:Hypergolic_fuel|hypergolic fuel combination]] is pressurized with [[w:Helium|helium]] during thrusting periods, so no propellant pump is needed. The propellant flow from the tanks to the thrust chamber is controlled by the engine injector valves, which are pneumatically controlled with [[w:Nitrogen|nitrogen]]. The engine is gimbaled to allow [[w:Thrust vectoring|Thrust Vector Control (TVC)]] during a burn. | ||
== Quickstart mode == | == Quickstart mode == | ||
In ''[[First Steps#Quickstart | In ''[[First Steps#Quickstart Mode|Quickstart Mode]]'' the SPS engine works like a normal Orbiter main thruster. The engine can be throttled with the keyboard or Orbiter's joystick control as usual, although the real SPS engine isn't throttleable. The [http://koti.mbnet.fi/jarmonik/Orbiter.html Interplanetary MFD (IMFD)] autoburn program can be used, too. It's not necessary to use the panel displays and controls, the Orbiter engine displays can be used, however the panel displays are enabled normally. | ||
== Engine thrust on/off logic == | == Engine thrust on/off logic == | ||
Line 11: | Line 11: | ||
[[Image:SPS_switch_location_3.jpg|thumb|350px|right|Location of SPS displays & controls on panel 1, lower part {{Panel label|name=1}}]] | [[Image:SPS_switch_location_3.jpg|thumb|350px|right|Location of SPS displays & controls on panel 1, lower part {{Panel label|name=1}}]] | ||
In | In ''[[First Steps#Virtual AGC Mode|Virtual AGC Mode]]'' the SPS engine works like the real thing, that means as specified in the original documentation<cite>AOH</cite>. So the real SPS engine isn't throttleable, it only can be turned on or off by opening or closing one or both of the two pairs of engine injector valves (bipropellant valve systems A or B) {{Panel label|name=3.D}} pneumatically. The gaseous nitrogen pressure of valve system A and B {{Panel label|name=3.B}} can be monitored by switching the SPS-PRESS IND switch {{Panel label|name=3.M}} to N<sub>2</sub> A or N<sub>2</sub> B. Each engine firing decreases the nitrogen pressure of the system used for the burn (A and/or B) by 50 psi<cite>A11_MISSIONREPORT</cite>, pressure at launch is 2500 psi. When the pressure of one system drops below 400 psi, the bipropellant valves of that system won't open anymore. | ||
In order to fire the SPS engine, the ΔV THRUST A and/or ΔV THRUST B switches {{Panel label|name=1.G}} are unguarded and switched to NORMAL ("single/double bank operation") to arm the control logic for engine injector valve system A or B.<cite> | In order to fire the SPS engine, the ΔV THRUST A and/or ΔV THRUST B switches {{Panel label|name=1.G}} are unguarded and switched to NORMAL ("single/double bank operation") to arm the control logic for engine injector valve system A or B.<cite>II</cite> During a burn the SPS chamber pressure can be monitored with the LV<sub>α</sub>/SPS P<sub>c</sub> indicator {{Panel label|name=1.B}}, when the LV/SPS IND switch {{Panel label|name=1.K}} is placed to P<sub>c</sub>. Normal chamber pressure is 100 psi. The remaining fuel and oxidizer quantity percentage in the tanks is shown by the corresponding indicator {{Panel label|name=3.E}}. | ||
There are 3 ways or thrust modes to fire the engine: | |||
=== SPS thrust direct on mode === | === SPS thrust direct on mode === | ||
The SPS engine is designed to be very reliable, so the easiest way to fire the engine, just in case everything else failed, is to switch the SPS THRUST switch {{Panel label|name=1.D}} to DIRECT ON. It can be stopped again by switching back to NORMAL. | The SPS engine is designed to be very reliable, so the easiest way to fire the engine, just in case everything else failed, is to switch the SPS THRUST switch {{Panel label|name=1.D}} to DIRECT ON. It can be stopped again by switching back to NORMAL. Please note that the engine doesn't stop, if the [[EMS]] is in ΔV mode and the EMS ΔV/RANGE display reads 0 ft/s or above while in SCS ΔV mode (see below). | ||
=== CMC ΔV mode === | === CMC ΔV mode === | ||
The normal way to control the SPS engine is to use the [[:Category:Apollo_Guidance_Computer|Command Module Computer]]. The [[Virtual AGC]] uses program P40 to both provide the thrust on signal and to control the SPS thrust vector. The [[ | The normal way to control the SPS engine is to use the [[:Category:Apollo_Guidance_Computer|Command Module Computer (CMC)]]. The [[Virtual AGC]] uses program P40 to both provide the thrust on signal and to control the SPS thrust vector. The [[Simple AGC]] has a couple of fictional programs to support the different mission phases. Anyway the SC CONT switch {{Panel label|name=1.A}} is switched to CMC and the [[THC]] isn't switched to CLOCKWISE. | ||
=== SCS ΔV mode === | === SCS ΔV mode === | ||
{{ | The SCS ΔV mode is obtained by positioning the SC CONT switch {{Panel label|name=1.A}} to SCS or by positioning the [[THC]] to CLOCKWISE. In this mode the burn is controlled by the [[EMS]] ΔV functions, so the EMS needs to be in ΔV mode and the EMS ΔV/RANGE display must above or equal to 0 ft/s, the [[EMS]] article explains how to configure the EMS for that. Thrust on is commanded by depressing the THRUST ON pushbutton {{Panel label|name=1.F}}. Once the burn has started the button can be released again. | ||
In reality a +X (foreward) translation command was necessary to start the burn in order to settle down the SPS propellants in the tanks before the burn. This can be done with the [[THC]] via the [[SCS]] as usual or by pressing the DIRECT ULLAGE pushbutton {{Panel label|name=1.E}}, which uses the direct thruster control coils<cite>III</cite>. This is not necessary in Project Apollo - NASSP though. | |||
When the EMS ΔV/RANGE display reads below 0 ft/s, the thrust is turned off. | |||
== Thrust vector control == | == Thrust vector control == | ||
In order to control a ΔV manoeuver the SPS engine can be gimbaled and change it's pitch and yaw gimbal angles to provide thrust vector control. Currently only the [[Virtual AGC]] | [[Image:SPS_switch_location_4.jpg|thumb|180px|right|Location of SPS displays & controls on panel 7 {{Panel label|name=7}}]] | ||
In order to control a ΔV manoeuver the SPS engine can be gimbaled and change it's pitch and yaw gimbal angles to provide thrust vector control. | |||
=== Gimbal Actuators === | |||
Thrust vector control is achieved by dual, servo, electromechanical actuators. Each actuator assembly (pitch and yaw) consists of four electromagnetic particle clutches, two DC motors and various gears to position the engine. One motor and a pair of clutches (extend and retract) are identified as system 1, the remaining motor and pair of clutches are identified as system 2 within the specific actuator (pitch and yaw). In order to use system 1 or 2 the clutches and gears need to be powered by switching the TVC SERVO POWER 1/2 switch {{Panel label|name=7.A}} to AC1/MNA or AC2/MNB<cite>IV</cite>. Each switch powers both the corresponding pitch and yaw system. | |||
Also the gimbal motors need to be turned on, each gimbal motor is controlled by its own SPS GIMBAL MOTOR switch, there are four SPS GIMBAL MOTOR switches, PITCH 1 and 2 and YAW 1 and 2 {{Panel label|name=1.J}}. When a SPS GIMBAL MOTOR switch is switched to START, the gimbal motor is started<cite>V</cite>. When the switch is released, it springs back to the center position, the motor is running. To turn off the motor the corresponing switch is switched back to OFF. | |||
Only one system, system 1 or 2, is used at a time to position the engine for each axis, pitch or yaw. Which system is used is determinated by the TVC GMBL DRIVE PITCH/YAW switches {{Panel label|name=1.M}}, see the switching table below. When switched to 1 or 2, system 1 or 2 is used. When switched to AUTO, system 1 is used except the [[THC]] is switched to CLOCKWISE, then system 2 is used. The overcurrent fail sense logic isn't implemented yet in Project Apollo - NASSP. | |||
The current SPS gimbal angles can be montitored by using the LV TANK PRESS/SPS GIMBAL meter {{Panel label|name=1.C}}, the -5°/+5° scale is used, provided that the LV/SPS IND switch {{Panel label|name=1.L}} is in GPI (Gimbal Position Indicator) position<cite>VI</cite>. | |||
=== TVC control modes === | |||
Similar to the engine thrust on/off logic there are three TVC control modes: CMC DAP, SCS AUTO TVC and MTVC (Manual Thrust Vector Control). | |||
[[image:SPS_TVC_switching.jpg|thumb|600px|none|The SPS TVC switching table<cite>AOH</cite>]] | |||
==== CMC DAP ==== | |||
Normally the [[:Category:Apollo_Guidance_Computer|Command Module Computer (CMC)]] is used for thrust vector control. In this mode the SPS gimbal angles are controlled by the CMC exclusively. Currently only the [[Virtual AGC]] has TVC capability, not the [[Simple AGC]]. Anyway the SC CONT switch {{Panel label|name=1.A}} is switched to CMC and the [[THC]] is switched to NEUTRAL for this configuration, see the switching table above. | |||
==== SCS AUTO TVC ==== | |||
Similar to the [[SCS]] attitude hold mode the SCS AUTO TVC mode insures that the thrust vector stays inertially fixed during the burn. Since that requires attitude error signals from [[BMAG]] 1, the gyro uncage logic must be satisfied. This requires that the BMAG MODE switches are in ATT 1/RATE 2, the ENTRY .05 G is OFF and that the SPS thrust on signal (see above) is present. Then the attitude of BMAG 1 is maintained by automatic control of the SPS gimbal angles. The current attitude error is shown by the [[CSM FDAI|FDAI]] in the BMAG1 error display mode. To enable this mode for the pitch or yaw axis, the SCS TVC PITCH or YAW switch {{Panel label|name=1.I}} is switched to AUTO and either the SC CONT switch {{Panel label|name=1.A}} is switched to SCS and the [[THC]] is switched to NEUTRAL, or SC CONT switch {{Panel label|name=1.A}} is switched to CMC and the [[THC]] is switched to CLOCKWISE, see the switching table above. | |||
In this mode the trim wheels {{Panel label|name=1.H}} on the LV TANK PRESS/SPS GIMBAL meter can be used to trim the CSM to compensate changes of the [[w:Center_of_mass|center of mass]], however this is not necessary in Project Apollo - NASSP. | |||
==== Manual Thrust Vector Control (MTVC) ==== | |||
Manual control of the thrust vector utilizes crew commands via the [[RHC]] to position the gimbaled SPS. There are two types of MTVC: MTVC with rate damping (rate command) and MTVC without rate damping (acceleration command). Either mode of MTVC is selectable by switching the SCS TVC PITCH or YAW switch {{Panel label|name=1.I}} to RATE CMD or ACCEL CMD with either the SC CONT switch {{Panel label|name=1.A}} switched to SCS and the [[THC]] switched to NEUTRAL, or SC CONT switch {{Panel label|name=1.A}} switched to CMC and the [[THC]] switched to CLOCKWISE. In addition, the THC CLOCKWISE logic provides an automatic transfer from the SCS AUTO TVC mode to the MTVC RATE CMD mode, see the switching table above. | |||
The RATE CMD configuration is analogous to the [[SCS]] proportional rate mode. With no manual input via the [[RHC]], the thrust vector is under rate BMAG control, the rate BMAG will drive the gimbals in the direction necessary to cancel any attitude rate. When an manual RHC input is present, a steady-state rate depending on the RHC deflection will be established. When the manual input is removed the rate is driven to zero. | |||
In ACCEL CMD configuration the rate feedback is inhibited and the RHC manual inputs control the SPS gimbal angles directly. That means the gimbal angels will change according to the RHC deflection, when the manual input is removed the gimbal angles remain constant and so the attitude acceleration. | |||
{{ | In this mode the trim wheels {{Panel label|name=1.H}} on the LV TANK PRESS/SPS GIMBAL meter can be used to trim the CSM to compensate changes of the [[w:Center_of_mass|center of mass]], however this is not necessary in Project Apollo - NASSP. | ||
== Propellant pressurization == | == Propellant pressurization == | ||
Line 41: | Line 79: | ||
[[Image:SPS_switch_location_1.jpg|thumb|180px|right|Location of SPS displays & controls on panel 3, upper part {{Panel label|name=3}}]] | [[Image:SPS_switch_location_1.jpg|thumb|180px|right|Location of SPS displays & controls on panel 3, upper part {{Panel label|name=3}}]] | ||
During a burn the fuel and oxidizer in the tanks are pressurized with helium to about | During a burn the fuel and oxidizer in the tanks are pressurized with helium to about 175 psi in order to press the propellants through the feed lines to the engine thrust chamber, where they ignite. The fuel and oxidizer tank pressure is shown by the SPS PRPLNT PRESS meters {{Panel label|name=3.C}}. The helium used for that is stored in the helium tanks, which pressure {{Panel label|name=3.B}} can be monitored by switching the SPS-PRESS IND switch {{Panel label|name=3.M}} to He. The fuel and oxidizer tanks are pressurized with the helium pressure regulator assemblies if one if the two SPS helium valves A/B are open. The helium valves are continuous-duty solenoid-operated and are energized open and spring-loaded closed. The SPS He VLV A/B switches {{Panel label|name=3.K}} permit automatic or manual control of the valves<cite>VII</cite>. With the switch in the AUTO position, the valves are automatically controlled by the thrust on/off signal, which is the default switch position. The valves are controlled manually by placing the switches to the ON (valve open) or OFF (valve closed) positions. Each valve position is shown by a talk-back indicator {{Panel label|name=3.K}} above each switch. When a valve is closed, the corresponding indicator is barber-pole(diagonal lines), the indication during non-SPS thrusting periods. When a valve is open, the the corresponding indicator is grey, the indication during SPS thrusting periods. | ||
The propellant pressurization can be tested with following procedure: | The propellant pressurization can be tested with following procedure: | ||
# It's assumed the CSM is flying free, has power supply and enough SPS propellants etc. Furthermore the SPS He VLV A/B switches {{Panel label|name=3.K}} are still placed to AUTO and the fuel and oxidizer pressure is fine, that means about | # It's assumed the CSM is flying free, has power supply and enough SPS propellants etc. Furthermore the SPS He VLV A/B switches {{Panel label|name=3.K}} are still placed to AUTO and the fuel and oxidizer pressure is fine, that means about 175 psi. | ||
# Start the SPS engine by switching the ΔV THRUST A switch {{Panel label|name=1.G}} to NORMAL and the SPS THRUST switch {{Panel label|name=1.D}} to DIRECT ON. The SPS He VLV A/B indicators {{Panel label|name=3.K}} change to grey indicating that the valves are opened automatically, the propellant pressures remain constant. | # Start the SPS engine by switching the ΔV THRUST A switch {{Panel label|name=1.G}} to NORMAL and the SPS THRUST switch {{Panel label|name=1.D}} to DIRECT ON. The SPS He VLV A/B indicators {{Panel label|name=3.K}} change to grey indicating that the valves are opened automatically, the propellant pressures remain constant. | ||
# Switch both SPS He VLV A/B switches {{Panel label|name=3.K}} to OFF. The SPS He VLV A/B indicators {{Panel label|name=3.K}} change to striped-line indication again indicating that the valves are closed. Depending on the propellant quantity the fuel and oxidizer pressure {{Panel label|name=3.C}} begins to decrease. When the tanks are full, the pressures drop rapidly. If the tanks are more empty, the pressures drop more slowly because of the bigger amount of helium in the tanks. Additionally the SPS chamber pressure {{Panel label|name=1.B}} begins to decrease and the thrust level decays. | # Switch both SPS He VLV A/B switches {{Panel label|name=3.K}} to OFF. The SPS He VLV A/B indicators {{Panel label|name=3.K}} change to striped-line indication again indicating that the valves are closed. Depending on the propellant quantity the fuel and oxidizer pressure {{Panel label|name=3.C}} begins to decrease. When the tanks are full, the pressures drop rapidly. If the tanks are more empty, the pressures drop more slowly because of the bigger amount of helium in the tanks. Additionally the SPS chamber pressure {{Panel label|name=1.B}} begins to decrease and the thrust level decays. | ||
# When the propellant pressure drops below | # When the propellant pressure drops below 157 psi, the [[Caution_and_Warning_System (CSM)|Caution & Warning System]] triggers the SPS PRESS alarm, press the MASTER ALARM pushbutton/light to turn off the alarm. | ||
# Switch one or both SPS He VLV A/B switches {{Panel label|name=3.K}} to AUTO again. The propellant and chamber pressures increase to the normal values and there's full thrust again. | # Switch one or both SPS He VLV A/B switches {{Panel label|name=3.K}} to AUTO again. The propellant and chamber pressures increase to the normal values and there's full thrust again. | ||
The procedure is | The procedure is no real test procedure, of course, normally the helium valves operate automatically during the mission. | ||
== Propellant utilization & gauging == | == Propellant utilization & gauging == | ||
Line 57: | Line 95: | ||
[[Image:SPS_switch_location_2.jpg|thumb|180px|right|Location of SPS displays & controls on panel 3, lower part {{Panel label|name=3}}]] | [[Image:SPS_switch_location_2.jpg|thumb|180px|right|Location of SPS displays & controls on panel 3, lower part {{Panel label|name=3}}]] | ||
The Propellant Utilization and Gauging Subsystem (PUGS) provides two important features, it measures the remaining fuel and oxidizer quantities and it displays and controls the fuel/oxidizer mixture ratio. Normal mixture ratio fuel:oxidizer is 1:1.6 and this is the initial propellant ratio in the tanks at the beginning of the mission, too. So when both the fuel and oxidizer quantity meters {{Panel label|name=3.E}} indicate the same percentage value, the propellants are balanced, the OXID UNBAL meter {{Panel label|name=3.F}} indicates 0lbs unbalance. | The Propellant Utilization and Gauging Subsystem (PUGS) provides two important features, it measures the remaining fuel and oxidizer quantities and it displays and controls the fuel/oxidizer mixture ratio.<cite>VIII</cite> Normal mixture ratio fuel:oxidizer is 1:1.6 and this is the initial propellant ratio in the tanks at the beginning of the mission, too. So when both the fuel and oxidizer quantity meters {{Panel label|name=3.E}} indicate the same percentage value, the propellants are balanced, the OXID UNBAL meter {{Panel label|name=3.F}} indicates 0lbs unbalance. | ||
=== Propellant Utilization Valve === | === Propellant Utilization Valve === | ||
If any unbalance | If any unbalance exists, which is determined from the INCR, DECR readings on the OXID UNBAL meter {{Panel label|name=3.F}}, the propellant utilization valve may be used to return the remaining propellants to a balanced condition. The propellant utilization valve, which is only powered<cite>VIII</cite> during a burn or a system test (see below), consists of a primary and secondary sliding gate valve. The OXID FLOW PRIM/SEC switch {{Panel label|name=3.I}} selects the primary or secondary valve for operation, normally the primary valve is used. When the unbalance meter shows INCR, the OXID FLOW VALVE switch {{Panel label|name=3.H}} is positioned to INCR, the sliding gate valve then moves to the increase flow position within 3.5 seconds. This will increase the oxidizer flow 3 percent above the nominal oxidizer flow, the upper OXID FLOW VALVE position indicator {{Panel label|name=3.H}} will indicate MAX, the lower indicator will remain gray. The secondary valve increases the oxidizer flow 6 percent above the nominal oxidizer flow. When the unbalance meter shows DECR, the OXID FLOW VALVE switch {{Panel label|name=3.H}} is positioned to DECR, the sliding gate valve then moves to the decrease flow position within 3.5 seconds. This will decrease the oxidizer flow 3.5 percent below the nominal oxidizer flow, the lower OXID FLOW VALVE position indicator {{Panel label|name=3.H}} will indicate MIN, the upper indicator will remain gray. The secondary valve decreases the oxidizer flow 7 percent below the nominal oxidizer flow. In Project Apollo - NASSP the propellants are balanced at the beginning, an unbalance can be created by positioning the OXID FLOW VALVE switch {{Panel label|name=3.H}} to INCR or DECR during a burn. | ||
=== Quantity gauging system test === | |||
The primary and auxiliary propellant gauging systems can be tested during the flight. With the PUG MODE switch {{Panel label|name=3.J}} in PRIM and the TEST switch {{Panel label|name=3.G}} in TEST 1 (up) position, the test stimuli are applied to the primary system after a time delay of 4 seconds driving the fuel and oxidizer readouts to an increased reading at different rates (except the tanks are full). This results in an unbalance and is so indicated on the unbalance meter {{Panel label|name=3.F}} as an INCR. When the TEST switch is released to center, the displays will lock at the readings that they had been driven to. With the TEST switch to TEST 2 position, after a time delay of 4 seconds the displays are driven back to the readings displayed prior to TEST 1. If the TEST switch is positioned to TEST 2 again, followed by the time delay of 4 seconds, the fuel and oxidizer readouts would drive to an decreased reading at different rates. This results in an unbalance and is so indicated on the unbalance meter as an DECR. To return to the readouts displayed prior to the second TEST 2, the TEST switch is positioned to TEST 1 and after the time delay of 4 seconds the displays return to the original values. | |||
To test the auxiliary system, the PUG MODE switch {{Panel label|name=3.J}} is positioned to AUX and the TEST switch {{Panel label|name=3.G}} is used the same way as explained above. But there are no time delays nor unbalanced test stimuli in the auxiliary test system, so the unbalance meter {{Panel label|name=3.F}} won't change it's reading. | |||
== Thermal control == | == Thermal control == | ||
[[Image:SPS propellant line.jpg|thumb|right|250px|Position of the SPS propellant feed lines]] | |||
The temperature of the propellant feed lines is indicated by the SPS PRPLNT TANKS TEMP meter {{Panel label|name=3.A}} and should be between 27 °F and 100 °F. A higher or lower temperature doesn't affect the SPS engine currently, but thermal control can be practiced. The propellant lines are cooled by radiation to space, if the temperature drops below 45 °F, the SPS LINE HTRS switch {{Panel label|name=3.L}} is placed to position A/B or A and 12 or 6 heater elements provide heat to the feed lines. The switch is placed to OFF when the temperature is raised to 75 °F. | |||
Additionally the propellant feed lines are heated by the sun and earth's or moon's albedo depending on the attitude and position of the spacecraft. The picture on the left shows the position on the spacecraft, where the feed lines receive maximum heat, in this case from the sun. If this part is exposed to the sun a long time, the temperature can raise too high and the attitude of the spacecraft needs to be changed. Also it's possible to put the spacecraft into a very slow roll motion, so that the propellant lines are heated periodically to a lower degree to keep the temperature within the limits without the heaters (Passive Thermal Control). | |||
<biblio force=false> | <biblio force=false> | ||
#I The ΔV THRUST A/B switches receive power from the SPS PILOT VLV MNA/B circuit breakers on panel 8 to supply the engine injector valve system A/B. They also receive power from the SPS HE VLV MNA/MNB circuit breakers to power the injector prevalves A/B. Additionally they apply power for the SPS ready signal to the CMC. | #I Real maximum vacuum thrust is about 20,700 lbf (92.1 kN). | ||
# | #II The ΔV THRUST A/B switches receive power from the SPS PILOT VLV MNA/B circuit breakers on panel 8 to supply the engine injector valve system A/B. They also receive power from the SPS HE VLV MNA/MNB circuit breakers to power the injector prevalves A/B. Additionally they apply power for the SPS ready signal to the CMC. | ||
# | #III The direct coils of RCS quad B and D receive DC power from the DIRECT ULL MNA circuit breaker on panel 8, RCS quad A and C receive DC power from the DIRECT ULL MNB circuit breaker. | ||
#IV TVC system 1 receives DC power from the SCS SYSTEM MNA circuit breaker and the AC power from the SCS TVC AC1 circuit breaker on panel 8 when switched to AC1/MNA. TVC system 1 receives DC power from the SCS SYSTEM MNB circuit breaker and the AC power from the SCS AC2 circuit breaker on panel 8 when switched to AC2/MNB. TVC system 2 receives DC power from the SCS SYSTEM MNA circuit breaker and the AC power from the SCS AC1 circuit breaker on panel 8 when switched to AC1/MNA. TVC system 2 receives DC power from the SCS SYSTEM MNB circuit breaker and the AC power from the SCS ECA/TVC AC2 circuit breaker on panel 8 when switched to AC2/MNB. | |||
#V The gimbal motors are started by motor-driven switches, which are supplied by the SPS PITCH 1 - BAT A, SPS PITCH 2 - BAT B, SPS YAW 1 - BAT A and SPS YAW 2 - BAT B circuit brakers on panel 8, which are supplied by BAT BUS A or B. The system 1/2 motors itself are powered by MAIN BUS A/B directly. | |||
#VI The GP/FPI meter power supply is controlled by the FDAI/GPI POWER switch on panel 7. Position 1 powers the first and third indicator via the SCS SYSTEM MNA and the SCS AC1 circuit breakers on panel 8, position 2 powers the second and fourth indicator via the SCS SYSTEM MNB and the SCS AC2 circuit breakers. In the BOTH position all indicators are energized. | |||
#VII The SPS He VLV A/B switches receive power from the SPS HE VLV MNA/MNB circuit breakers on panel 8 to supply the helium valves A/B. | |||
#VIII The propellant gauging system and the propellant utilization valve receive DC power from both the SPS GAUGING MNA and MNB circuit breakers on panel 8 and AC power from either the SPS GAUGING AC 1 or AC 2 circuit breakers on panel 8 depending on the SPS GAUGING switch on panel 4. | |||
#[[References]] | #[[References]] | ||
</biblio> | |||
==External Links== | ==External Links== |
Latest revision as of 11:01, 29 July 2008

The Service Propulsion System (SPS) is the Command/Service Module main engine and provides the impulse for all velocity changes (ΔVs) throughout a mission and the SPS abort capability after the launch escape tower is jettisoned. The engine uses Aerozine 50 (hydrazine/UDMH) fuel and nitrogen tetroxide oxidizer and has a nominal thrust of 20,500 lbf (91.2 kN)I. This hypergolic fuel combination is pressurized with helium during thrusting periods, so no propellant pump is needed. The propellant flow from the tanks to the thrust chamber is controlled by the engine injector valves, which are pneumatically controlled with nitrogen. The engine is gimbaled to allow Thrust Vector Control (TVC) during a burn.
Quickstart mode
In Quickstart Mode the SPS engine works like a normal Orbiter main thruster. The engine can be throttled with the keyboard or Orbiter's joystick control as usual, although the real SPS engine isn't throttleable. The Interplanetary MFD (IMFD) autoburn program can be used, too. It's not necessary to use the panel displays and controls, the Orbiter engine displays can be used, however the panel displays are enabled normally.
Engine thrust on/off logic
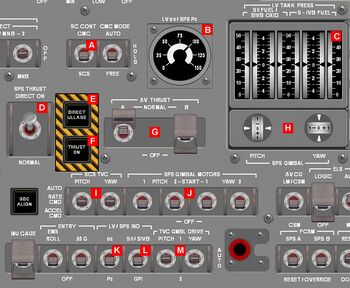
In Virtual AGC Mode the SPS engine works like the real thing, that means as specified in the original documentationAOH. So the real SPS engine isn't throttleable, it only can be turned on or off by opening or closing one or both of the two pairs of engine injector valves (bipropellant valve systems A or B) 3.D pneumatically. The gaseous nitrogen pressure of valve system A and B 3.B can be monitored by switching the SPS-PRESS IND switch 3.M to N2 A or N2 B. Each engine firing decreases the nitrogen pressure of the system used for the burn (A and/or B) by 50 psiA11_MISSIONREPORT, pressure at launch is 2500 psi. When the pressure of one system drops below 400 psi, the bipropellant valves of that system won't open anymore.
In order to fire the SPS engine, the ΔV THRUST A and/or ΔV THRUST B switches 1.G are unguarded and switched to NORMAL ("single/double bank operation") to arm the control logic for engine injector valve system A or B.II During a burn the SPS chamber pressure can be monitored with the LVα/SPS Pc indicator 1.B, when the LV/SPS IND switch 1.K is placed to Pc. Normal chamber pressure is 100 psi. The remaining fuel and oxidizer quantity percentage in the tanks is shown by the corresponding indicator 3.E.
There are 3 ways or thrust modes to fire the engine:
SPS thrust direct on mode
The SPS engine is designed to be very reliable, so the easiest way to fire the engine, just in case everything else failed, is to switch the SPS THRUST switch 1.D to DIRECT ON. It can be stopped again by switching back to NORMAL. Please note that the engine doesn't stop, if the EMS is in ΔV mode and the EMS ΔV/RANGE display reads 0 ft/s or above while in SCS ΔV mode (see below).
CMC ΔV mode
The normal way to control the SPS engine is to use the Command Module Computer (CMC). The Virtual AGC uses program P40 to both provide the thrust on signal and to control the SPS thrust vector. The Simple AGC has a couple of fictional programs to support the different mission phases. Anyway the SC CONT switch 1.A is switched to CMC and the THC isn't switched to CLOCKWISE.
SCS ΔV mode
The SCS ΔV mode is obtained by positioning the SC CONT switch 1.A to SCS or by positioning the THC to CLOCKWISE. In this mode the burn is controlled by the EMS ΔV functions, so the EMS needs to be in ΔV mode and the EMS ΔV/RANGE display must above or equal to 0 ft/s, the EMS article explains how to configure the EMS for that. Thrust on is commanded by depressing the THRUST ON pushbutton 1.F. Once the burn has started the button can be released again.
In reality a +X (foreward) translation command was necessary to start the burn in order to settle down the SPS propellants in the tanks before the burn. This can be done with the THC via the SCS as usual or by pressing the DIRECT ULLAGE pushbutton 1.E, which uses the direct thruster control coilsIII. This is not necessary in Project Apollo - NASSP though.
When the EMS ΔV/RANGE display reads below 0 ft/s, the thrust is turned off.
Thrust vector control
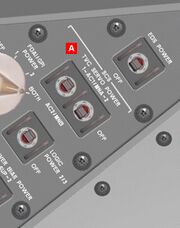
In order to control a ΔV manoeuver the SPS engine can be gimbaled and change it's pitch and yaw gimbal angles to provide thrust vector control.
Gimbal Actuators
Thrust vector control is achieved by dual, servo, electromechanical actuators. Each actuator assembly (pitch and yaw) consists of four electromagnetic particle clutches, two DC motors and various gears to position the engine. One motor and a pair of clutches (extend and retract) are identified as system 1, the remaining motor and pair of clutches are identified as system 2 within the specific actuator (pitch and yaw). In order to use system 1 or 2 the clutches and gears need to be powered by switching the TVC SERVO POWER 1/2 switch 7.A to AC1/MNA or AC2/MNBIV. Each switch powers both the corresponding pitch and yaw system.
Also the gimbal motors need to be turned on, each gimbal motor is controlled by its own SPS GIMBAL MOTOR switch, there are four SPS GIMBAL MOTOR switches, PITCH 1 and 2 and YAW 1 and 2 1.J. When a SPS GIMBAL MOTOR switch is switched to START, the gimbal motor is startedV. When the switch is released, it springs back to the center position, the motor is running. To turn off the motor the corresponing switch is switched back to OFF.
Only one system, system 1 or 2, is used at a time to position the engine for each axis, pitch or yaw. Which system is used is determinated by the TVC GMBL DRIVE PITCH/YAW switches 1.M, see the switching table below. When switched to 1 or 2, system 1 or 2 is used. When switched to AUTO, system 1 is used except the THC is switched to CLOCKWISE, then system 2 is used. The overcurrent fail sense logic isn't implemented yet in Project Apollo - NASSP.
The current SPS gimbal angles can be montitored by using the LV TANK PRESS/SPS GIMBAL meter 1.C, the -5°/+5° scale is used, provided that the LV/SPS IND switch 1.L is in GPI (Gimbal Position Indicator) positionVI.
TVC control modes
Similar to the engine thrust on/off logic there are three TVC control modes: CMC DAP, SCS AUTO TVC and MTVC (Manual Thrust Vector Control).
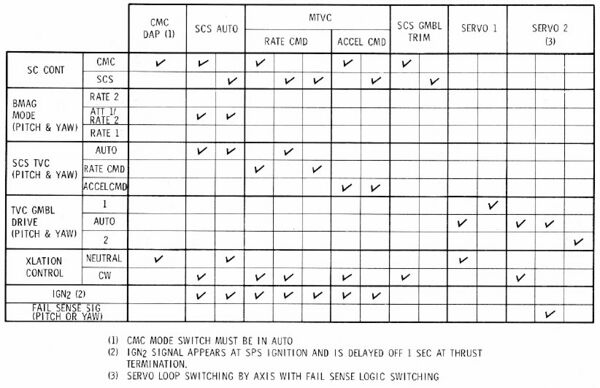
CMC DAP
Normally the Command Module Computer (CMC) is used for thrust vector control. In this mode the SPS gimbal angles are controlled by the CMC exclusively. Currently only the Virtual AGC has TVC capability, not the Simple AGC. Anyway the SC CONT switch 1.A is switched to CMC and the THC is switched to NEUTRAL for this configuration, see the switching table above.
SCS AUTO TVC
Similar to the SCS attitude hold mode the SCS AUTO TVC mode insures that the thrust vector stays inertially fixed during the burn. Since that requires attitude error signals from BMAG 1, the gyro uncage logic must be satisfied. This requires that the BMAG MODE switches are in ATT 1/RATE 2, the ENTRY .05 G is OFF and that the SPS thrust on signal (see above) is present. Then the attitude of BMAG 1 is maintained by automatic control of the SPS gimbal angles. The current attitude error is shown by the FDAI in the BMAG1 error display mode. To enable this mode for the pitch or yaw axis, the SCS TVC PITCH or YAW switch 1.I is switched to AUTO and either the SC CONT switch 1.A is switched to SCS and the THC is switched to NEUTRAL, or SC CONT switch 1.A is switched to CMC and the THC is switched to CLOCKWISE, see the switching table above.
In this mode the trim wheels 1.H on the LV TANK PRESS/SPS GIMBAL meter can be used to trim the CSM to compensate changes of the center of mass, however this is not necessary in Project Apollo - NASSP.
Manual Thrust Vector Control (MTVC)
Manual control of the thrust vector utilizes crew commands via the RHC to position the gimbaled SPS. There are two types of MTVC: MTVC with rate damping (rate command) and MTVC without rate damping (acceleration command). Either mode of MTVC is selectable by switching the SCS TVC PITCH or YAW switch 1.I to RATE CMD or ACCEL CMD with either the SC CONT switch 1.A switched to SCS and the THC switched to NEUTRAL, or SC CONT switch 1.A switched to CMC and the THC switched to CLOCKWISE. In addition, the THC CLOCKWISE logic provides an automatic transfer from the SCS AUTO TVC mode to the MTVC RATE CMD mode, see the switching table above.
The RATE CMD configuration is analogous to the SCS proportional rate mode. With no manual input via the RHC, the thrust vector is under rate BMAG control, the rate BMAG will drive the gimbals in the direction necessary to cancel any attitude rate. When an manual RHC input is present, a steady-state rate depending on the RHC deflection will be established. When the manual input is removed the rate is driven to zero.
In ACCEL CMD configuration the rate feedback is inhibited and the RHC manual inputs control the SPS gimbal angles directly. That means the gimbal angels will change according to the RHC deflection, when the manual input is removed the gimbal angles remain constant and so the attitude acceleration.
In this mode the trim wheels 1.H on the LV TANK PRESS/SPS GIMBAL meter can be used to trim the CSM to compensate changes of the center of mass, however this is not necessary in Project Apollo - NASSP.
Propellant pressurization
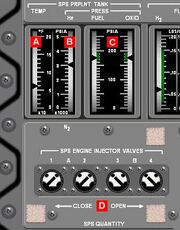
During a burn the fuel and oxidizer in the tanks are pressurized with helium to about 175 psi in order to press the propellants through the feed lines to the engine thrust chamber, where they ignite. The fuel and oxidizer tank pressure is shown by the SPS PRPLNT PRESS meters 3.C. The helium used for that is stored in the helium tanks, which pressure 3.B can be monitored by switching the SPS-PRESS IND switch 3.M to He. The fuel and oxidizer tanks are pressurized with the helium pressure regulator assemblies if one if the two SPS helium valves A/B are open. The helium valves are continuous-duty solenoid-operated and are energized open and spring-loaded closed. The SPS He VLV A/B switches 3.K permit automatic or manual control of the valvesVII. With the switch in the AUTO position, the valves are automatically controlled by the thrust on/off signal, which is the default switch position. The valves are controlled manually by placing the switches to the ON (valve open) or OFF (valve closed) positions. Each valve position is shown by a talk-back indicator 3.K above each switch. When a valve is closed, the corresponding indicator is barber-pole(diagonal lines), the indication during non-SPS thrusting periods. When a valve is open, the the corresponding indicator is grey, the indication during SPS thrusting periods.
The propellant pressurization can be tested with following procedure:
- It's assumed the CSM is flying free, has power supply and enough SPS propellants etc. Furthermore the SPS He VLV A/B switches 3.K are still placed to AUTO and the fuel and oxidizer pressure is fine, that means about 175 psi.
- Start the SPS engine by switching the ΔV THRUST A switch 1.G to NORMAL and the SPS THRUST switch 1.D to DIRECT ON. The SPS He VLV A/B indicators 3.K change to grey indicating that the valves are opened automatically, the propellant pressures remain constant.
- Switch both SPS He VLV A/B switches 3.K to OFF. The SPS He VLV A/B indicators 3.K change to striped-line indication again indicating that the valves are closed. Depending on the propellant quantity the fuel and oxidizer pressure 3.C begins to decrease. When the tanks are full, the pressures drop rapidly. If the tanks are more empty, the pressures drop more slowly because of the bigger amount of helium in the tanks. Additionally the SPS chamber pressure 1.B begins to decrease and the thrust level decays.
- When the propellant pressure drops below 157 psi, the Caution & Warning System triggers the SPS PRESS alarm, press the MASTER ALARM pushbutton/light to turn off the alarm.
- Switch one or both SPS He VLV A/B switches 3.K to AUTO again. The propellant and chamber pressures increase to the normal values and there's full thrust again.
The procedure is no real test procedure, of course, normally the helium valves operate automatically during the mission.
Propellant utilization & gauging

The Propellant Utilization and Gauging Subsystem (PUGS) provides two important features, it measures the remaining fuel and oxidizer quantities and it displays and controls the fuel/oxidizer mixture ratio.VIII Normal mixture ratio fuel:oxidizer is 1:1.6 and this is the initial propellant ratio in the tanks at the beginning of the mission, too. So when both the fuel and oxidizer quantity meters 3.E indicate the same percentage value, the propellants are balanced, the OXID UNBAL meter 3.F indicates 0lbs unbalance.
Propellant Utilization Valve
If any unbalance exists, which is determined from the INCR, DECR readings on the OXID UNBAL meter 3.F, the propellant utilization valve may be used to return the remaining propellants to a balanced condition. The propellant utilization valve, which is only poweredVIII during a burn or a system test (see below), consists of a primary and secondary sliding gate valve. The OXID FLOW PRIM/SEC switch 3.I selects the primary or secondary valve for operation, normally the primary valve is used. When the unbalance meter shows INCR, the OXID FLOW VALVE switch 3.H is positioned to INCR, the sliding gate valve then moves to the increase flow position within 3.5 seconds. This will increase the oxidizer flow 3 percent above the nominal oxidizer flow, the upper OXID FLOW VALVE position indicator 3.H will indicate MAX, the lower indicator will remain gray. The secondary valve increases the oxidizer flow 6 percent above the nominal oxidizer flow. When the unbalance meter shows DECR, the OXID FLOW VALVE switch 3.H is positioned to DECR, the sliding gate valve then moves to the decrease flow position within 3.5 seconds. This will decrease the oxidizer flow 3.5 percent below the nominal oxidizer flow, the lower OXID FLOW VALVE position indicator 3.H will indicate MIN, the upper indicator will remain gray. The secondary valve decreases the oxidizer flow 7 percent below the nominal oxidizer flow. In Project Apollo - NASSP the propellants are balanced at the beginning, an unbalance can be created by positioning the OXID FLOW VALVE switch 3.H to INCR or DECR during a burn.
Quantity gauging system test
The primary and auxiliary propellant gauging systems can be tested during the flight. With the PUG MODE switch 3.J in PRIM and the TEST switch 3.G in TEST 1 (up) position, the test stimuli are applied to the primary system after a time delay of 4 seconds driving the fuel and oxidizer readouts to an increased reading at different rates (except the tanks are full). This results in an unbalance and is so indicated on the unbalance meter 3.F as an INCR. When the TEST switch is released to center, the displays will lock at the readings that they had been driven to. With the TEST switch to TEST 2 position, after a time delay of 4 seconds the displays are driven back to the readings displayed prior to TEST 1. If the TEST switch is positioned to TEST 2 again, followed by the time delay of 4 seconds, the fuel and oxidizer readouts would drive to an decreased reading at different rates. This results in an unbalance and is so indicated on the unbalance meter as an DECR. To return to the readouts displayed prior to the second TEST 2, the TEST switch is positioned to TEST 1 and after the time delay of 4 seconds the displays return to the original values.
To test the auxiliary system, the PUG MODE switch 3.J is positioned to AUX and the TEST switch 3.G is used the same way as explained above. But there are no time delays nor unbalanced test stimuli in the auxiliary test system, so the unbalance meter 3.F won't change it's reading.
Thermal control
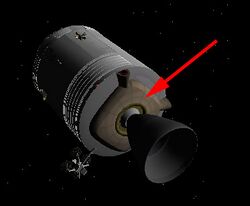
The temperature of the propellant feed lines is indicated by the SPS PRPLNT TANKS TEMP meter 3.A and should be between 27 °F and 100 °F. A higher or lower temperature doesn't affect the SPS engine currently, but thermal control can be practiced. The propellant lines are cooled by radiation to space, if the temperature drops below 45 °F, the SPS LINE HTRS switch 3.L is placed to position A/B or A and 12 or 6 heater elements provide heat to the feed lines. The switch is placed to OFF when the temperature is raised to 75 °F.
Additionally the propellant feed lines are heated by the sun and earth's or moon's albedo depending on the attitude and position of the spacecraft. The picture on the left shows the position on the spacecraft, where the feed lines receive maximum heat, in this case from the sun. If this part is exposed to the sun a long time, the temperature can raise too high and the attitude of the spacecraft needs to be changed. Also it's possible to put the spacecraft into a very slow roll motion, so that the propellant lines are heated periodically to a lower degree to keep the temperature within the limits without the heaters (Passive Thermal Control).
<biblio force=false>
#I Real maximum vacuum thrust is about 20,700 lbf (92.1 kN). #II The ΔV THRUST A/B switches receive power from the SPS PILOT VLV MNA/B circuit breakers on panel 8 to supply the engine injector valve system A/B. They also receive power from the SPS HE VLV MNA/MNB circuit breakers to power the injector prevalves A/B. Additionally they apply power for the SPS ready signal to the CMC. #III The direct coils of RCS quad B and D receive DC power from the DIRECT ULL MNA circuit breaker on panel 8, RCS quad A and C receive DC power from the DIRECT ULL MNB circuit breaker. #IV TVC system 1 receives DC power from the SCS SYSTEM MNA circuit breaker and the AC power from the SCS TVC AC1 circuit breaker on panel 8 when switched to AC1/MNA. TVC system 1 receives DC power from the SCS SYSTEM MNB circuit breaker and the AC power from the SCS AC2 circuit breaker on panel 8 when switched to AC2/MNB. TVC system 2 receives DC power from the SCS SYSTEM MNA circuit breaker and the AC power from the SCS AC1 circuit breaker on panel 8 when switched to AC1/MNA. TVC system 2 receives DC power from the SCS SYSTEM MNB circuit breaker and the AC power from the SCS ECA/TVC AC2 circuit breaker on panel 8 when switched to AC2/MNB. #V The gimbal motors are started by motor-driven switches, which are supplied by the SPS PITCH 1 - BAT A, SPS PITCH 2 - BAT B, SPS YAW 1 - BAT A and SPS YAW 2 - BAT B circuit brakers on panel 8, which are supplied by BAT BUS A or B. The system 1/2 motors itself are powered by MAIN BUS A/B directly. #VI The GP/FPI meter power supply is controlled by the FDAI/GPI POWER switch on panel 7. Position 1 powers the first and third indicator via the SCS SYSTEM MNA and the SCS AC1 circuit breakers on panel 8, position 2 powers the second and fourth indicator via the SCS SYSTEM MNB and the SCS AC2 circuit breakers. In the BOTH position all indicators are energized. #VII The SPS He VLV A/B switches receive power from the SPS HE VLV MNA/MNB circuit breakers on panel 8 to supply the helium valves A/B. #VIII The propellant gauging system and the propellant utilization valve receive DC power from both the SPS GAUGING MNA and MNB circuit breakers on panel 8 and AC power from either the SPS GAUGING AC 1 or AC 2 circuit breakers on panel 8 depending on the SPS GAUGING switch on panel 4. #References
</biblio>